WHAT IS AN AIR RECEIVER USED FOR?
An Air Receiver or ‘compressed air tank’ as it can commonly be referred to is an important part of any compressed air system as its primary purpose is to receive and store compressed air after it exits the air compressor. This gives you a reserve of compressed air that can be used without running your air compressor, and it also helps to minimize unstable peaks in compressed air pressure which is vital to the efficient running of an air compressor system.
In this blog, you’ll learn more about what an air receiver does, what it’s typically used for, and the different types of air receivers available.
Read on to learn more about this important piece of compressed air system equipment.
What is an air receiver?
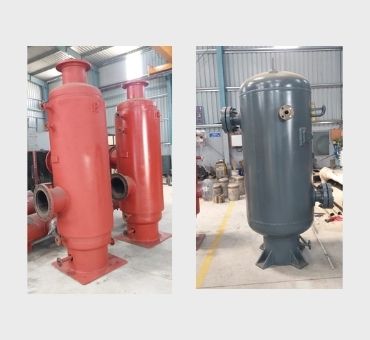
As we’ve already alluded to, air receivers play a vital part in the effective operation of a compressed air system. An air receiver tank is a type of pressure vessel, which acts to provide storage for compressed air to assist with peak demands in your compressed air system; an air receiver also helps to control and stabilise air system pressure.
Air receivers come in a range of sizes, in both vertical and horizontal configurations. Depending on the usage, they can be supplied in paint finish, galvanised steel, or stainless steel.
An air receiver is a vital part of a compressed air system.
Why use an air receiver?
While your compressed air could potentially run without the need for an air receiver, the general rule of thumb is that air receivers should be used in every compressed air system. As the need for compressed air in a factory or plant can vary drastically throughout the day depending on processing requirements, compressed air needs or unusual demands, an air receiver is crucial in regulating these changes and demands. An air receiver will provide storage to account for short-term peaks in air demand that an air compressor could not manage.
Not having an air receiver as a part of your compressed air system could lead to more loading and unloading cycles which will push your compressor to work harder than it needs to, to get the job done. An air receiver can ensure a stable supply of compressed air even when demand changes throughout the day.
In some industries like the wine industry, large air receivers are used for storage to enable a lower capital investment cost to plant and equipment. Wineries typically require a very large amount of compressed air to operate the wine presses several times a day, during the manufacturing process. However, this is only for a short period of the year, and it is far more cost-effective to purchase multiple large air receivers to accumulate and store compressed air than it is to invest in a compressor large enough for their requirements. It also means the business is not paying to run an over-sized compressor for their daily operating during the remainder of the year.
Large pressure vessels can also be used in the same way for storage of nitrogen or oxygen.
Important considerations for air receivers
Output pressure
As we’ve outlined previously, an air receiver can be used to minimise unstable peaks in your compressed air pressure, allowing you to reduce the overall pressure at which your air compressor operates. Without plenty of storage to draw on, the system will have to operate at higher pressures so it’s always ready to meet peak demands.
Compressed air that ends up being stored in your air receiver tank will only be useful if the output pressure is sufficient for the process in which it will be used. You will need to consider the amount of time that the air receiver can supply air at the necessary pressure for your equipment.
Increase efficiency of the dryer
If your air receiver is placed before the dryer (‘wet tank’) it can help to improve the efficiency of your air dryer. Air from the compressor is very hot, and therefore moisture-laden. As the air passes through the air receiver, it cools – cool air holds less moisture than hot air, so excess moisture condenses and falls out of the air as a liquid. This liquid drains out of a valve at the bottom of the air receiver, and by removing some of the moisture in advance, it reduces the amount of work the dryer needs to do. This improved efficiency provides additional energy savings for your system.
Wet or dry storage – what’s the difference?
‘Wet’ storage tanks are located before the air drying system. ‘Dry’ storage tanks are located after the air dryer and are used to store air that is already dried and filtered.
So what’s best? There are several advantages for both, and sometimes it comes down to personal preference. It is best to consult the experts and discuss your particular requirements, but for many applications, it makes sense to have a combination of the two. The ideal ratio of compressed air storage is ⅓ wet to ⅔ dry capacity.
Advantages of wet compressed air storage
As already mentioned, with wet air storage, the air receiver is positioned in between the air compressor and the air dryer. Hot, wet air enters the receiver tank from the compressor through the lower inlet port in the tank and exits through the upper port to enter the drying system. A wet air receiver has several benefits:
- It increases the efficiency of your dryer by allowing excess water and lubricant to condense out of the air before it enters the dryer.
- It prolongs the life of the pre-filter element, which is located between the wet storage receiver and the dryer since the air going through the filter is cleaner and dryer than if it was coming straight out of the compressor.
The downside to a wet air receiver is that the moisture inside the receiver can cause it to corrode, and the air receiver may not last as long as expected.
Advantages of dry compressed air storage
A dry air storage tank has advantages as well – dry compressed air is ready to be used straight out of the tank.
Without a dry air tank to store ready-to-use air, air from the wet tank will need to go through the air dryer before being used. During periods of high demand, the system may try to pull air through at higher volumes than the dryer is capable of. If it can’t keep up with demand, drying efficiency is reduced, leading to unwanted moisture in the air lines.
In addition, as in the case of wineries, or other industries with large variances in compressed air needs, having one or more correctly sized dry receivers is the only solution for bulk compressed air storage.
The size of the air receiver
Air receivers can come in many different sizes and both vertical and horizontal orientations so it’s not a ‘one size fits all’ when it comes to selecting an air receiver for your compressed air system.
Many recommend that when choosing an air receiver that’s the right size for your needs you should allow for between 10 to 15 litres of tank volume for each CFM of compressed air. This may vary depending on the compressed air system you have in place, and your compressed air use, however, this calculation can be a good starting point.
The location of your air receiver
Where space is limited for additional equipment in a factory or processing plant then the location of your air receiver matters. If you have a smaller air compressor, a lot of these come already mounted on top of an air receiver (integrated), which saves on valuable floor space. However, with larger compressors (usually 25HP and over), this is not an option. Sometimes several receivers are a good idea, with a larger storage receiver being placed near the air compressor, and smaller receivers being placed nearer the points-of-use.
Air receivers can be situated outside but should have frequent inspections to monitor for corrosion. Any signs of corrosion should be addressed immediately to maintain the integrity of the tank.
Draining an air receiver
Many are unaware that moisture can collect inside an air receiver tank if your compressed air system doesn’t include an air dryer. Too much moisture inside an air receiver tank will lead to corrosion of the air receiver, blocked piping and damage to your pneumatic equipment – all of these factors can then have a knock-on effect and could result in damage to your product or processing.
An air receiver should be drained daily to avoid any potential damage. Automatic condensate drains can be used to avoid this and release any moisture build-up.
Steel, galvanised or stainless steel tank?
The majority of air receivers are bare steel on the inside with a specially formulated coating on the outside to reduce corrosion. The exterior paint is often colour-matched for the type of gas, blue for compressed air, green for nitrogen, or white for oxygen. A basic steel tank works well for most applications and is the least expensive option. However, they may be prone to corrosion if too much liquid is allowed to build up inside the tank, and are not suitable for food-grade production facilities.
Galvanised air receivers are treated inside and out with a protective zinc coating to halt the formation of rust. Zinc protects the base metal by reacting chemically with corrosive agents before they can reach the base. Galvanised tanks are better at maintaining air purity because they reduce the risk of particulates caused by corrosion entering the air supply.
Stainless steel air receivers are primarily used in applications where very high purity air is required. They are the most expensive option but are highly durable and corrosion-resistant. Hospitals, labs, electronics manufacturers, food producers and other applications requiring high-purity air supply should consider a stainless steel tank.
What accessories should be used?
Correctly rated air accessories are essential for tank safety and operation. While the receiver itself is just a large sealed metal tube, it is a pressurised vessel, and at a minimum must have:
- A pressure gauge to monitor the interior pressure.
- A safety relief valve.
- A drain to release excess liquid building up inside the receiver.